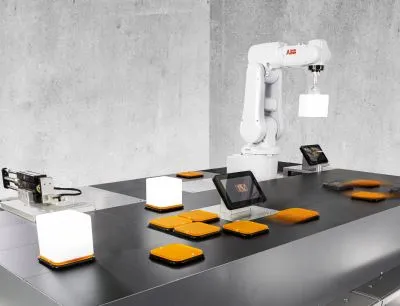
With Acopos 6D, B&R heralds a new era of manufacturing. Magnetic levitating shuttles move individual products freely through the machine. Gone are the days when conventional transport systems imposed rigidly defined timing on the production process. Acopos 6D is ideal for small-batch production with frequent changeover between products of different designs and dimensions. Acopos 6D is based on the principle of magnetic levitation: Shuttles with integrated permanent magnets float over the surface of electromagnetic motor segments. The modular motor segments are 240 x 240 millimeters in size and can be arranged freely in any shape. A variety of shuttle sizes carry payloads of 0.6 to 14 kilograms and reach speeds of up to 2 meters per second. They can move freely in two-dimensional space, rotate and tilt along three axes and offer precise control over the height of levitation. All together, that gives them six degrees of motion control freedom.
Space savings and zero wear
Acopos 6D offers up to four times the shuttle density of other systems on the market through the unique ability to control four shuttles on the same motor segment simultaneously. The shuttles can also be used as axes in processing stations. An Acopos 6D shuttle carrying a workpiece could follow a CNC path, for example, allowing the processing tool to be mounted rigidly. Weighing stations can be eliminated entirely, since each shuttle can also serve as a high-precision scale. This makes it possible to design a more compact machine. Acopos 6D shuttles levitate freely without any contact or friction. With no abrasive wear, there are no parts to be maintained. If a stainless steel cover is placed over the motor segments, Acopos 6D offers IP69K protection - making it ideally suited for cleanrooms or food and beverage production.
Acopos 6D is fully integrated in the B&R ecosystem. That allows the shuttles to be synchronized with servo axes, robots, track systems and machine vision cameras with microsecond precision. Path planning for the shuttles occurs in a dedicated controller, connected to the machine network via Powerlink - which means it has no impact on the performance of the network or machine control system. For systems with more than 200 segments or 50 shuttles, multiple controllers can be synchronized with each other.
Intelligent shuttles and easy setup
Unlike comparable systems, each Acopos 6D shuttle is assigned a globally unique ID. At startup, the controller immediately knows the location of each shuttle on the motor segments, and production can begin without time-consuming homing sequences or manual input by an operator. The shuttles offer a positioning repeatability of ±5 µm, making Acopos 6D perfectly suited for applications with strict positioning requirements, like those in the electronics industry and in the assembly of mechanical and electronic components.
Acopos 6D offers nearly limitless possibilities in machine design, yet is remarkably easy to set up. Sophisticated algorithms ensure the shuttles follow an optimal path while avoiding collisions and minimizing energy consumption. Developers are free to concentrate on their primary task: developing optimal machine processes that deliver maximum productivity. Acopos 6D was developed in cooperation with Planar Motors Inc., a company with more than 15 years of research and development in the field of magnetic levitation technology for industrial manufacturing. B&R is a shareholder in Planar Motors.